Carbon In Leach (CIL) and Carbon In Pulp (CIP) are two commonly used methods in the gold extraction process. Although both methods involve the use of activated carbon to adsorb gold, there are significant differences in their operation processes, equipment layout, and application conditions. This article will explore the differences between CIL and CIP, highlighting their respective advantages, disadvantages.
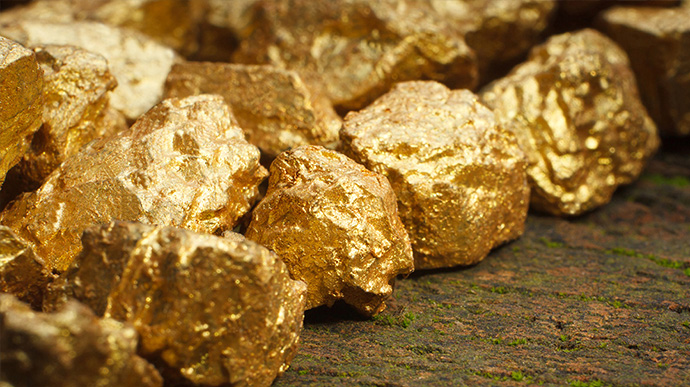
1. Basic Principles
1.1 Carbon In Leach (CIL)
The Carbon In Leach (CIL) process involves adding activated carbon directly into the leaching tanks where both leaching and adsorption occur simultaneously. The CIL process includes the following steps:
Crushing and grinding the gold ore into a pulp.
Mixing the pulp with sodium cyanide solution to dissolve the gold into a cyanide complex.
Adding activated carbon to the pulp during the leaching process, where the activated carbon adsorbs the dissolved gold.
After leaching and adsorption, the pulp undergoes solid-liquid separation to recover the gold-laden activated carbon.
The gold-laden activated carbon undergoes desorption and electrolysis to recover the gold.
1.2 Carbon In Pulp (CIP)
The Carbon In Pulp (CIP) process differs primarily in the timing of adding activated carbon. The CIP process includes:
Crushing and grinding the gold ore into a pulp.
Mixing the pulp with sodium cyanide solution to dissolve the gold into a cyanide complex.
After leaching, transferring the pulp to a series of adsorption tanks where activated carbon is sequentially added to adsorb the dissolved gold.
After adsorption, the pulp undergoes solid-liquid separation to recover the gold-laden activated carbon.
The gold-laden activated carbon undergoes desorption and electrolysis to recover the gold.
2. Main Differences
2.1 Process Differences
Simultaneous Leaching and Adsorption: In CIL, leaching and adsorption occur simultaneously in the same step, whereas in CIP, leaching occurs first, followed by adsorption.
Process Complexity: CIP has a relatively simpler process because leaching and adsorption are separate steps. CIL requires more precise control of process parameters as leaching and adsorption occur concurrently, making it more complex to operate.
2.2 Equipment Configuration
CIL: Since leaching and adsorption occur in the same tank, CIL requires fewer tanks, but each tank is larger and more complex in design.
CIP: CIP requires separate leaching and adsorption tanks. Although there are more tanks, each tank is simpler in design and offers greater operational flexibility.
2.3 Gold Ore Characteristics
Ore Type Suitability: CIL is more suitable for low-grade, high-clay-content ores as these ores can clog the leaching tanks during processing. CIL’s design can better handle this issue. CIP is more suitable for high-grade, uniformly sized ores.
Pulp Handling Capacity: CIL requires stricter control over pulp concentration and particle size, while CIP is relatively more forgiving.
3. Advantages and Disadvantages
3.1 CIL Advantages and Disadvantages
Advantages:
Simultaneous leaching and adsorption result in a shorter process with faster reaction times.
Better suited for high-clay-content ores.
Disadvantages:
Requires precise control of leaching and adsorption process parameters, making it complex to operate.
Higher initial investment due to more demanding equipment and process design.
3.2 CIP Advantages and Disadvantages
Advantages:
Simple process with high operational flexibility.
Adsorption tanks can be used in series, improving adsorption efficiency.
Suitable for high-grade gold ores with simpler process control.
Disadvantages:
Requires separate leaching and adsorption tanks, occupying more space.
Less effective for high-clay-content ores.
The determination of the gold ore extraction process requires strict extraction tests and is determined by professionals. If you have any gold ore extraction needs, please leave a message below, one engineer from our team will contact you shortly.